New dimensions: Harnessing additive manufacturing
Claire Burrows, partner in the regulatory and professional conduct team and Colin Bell, partner and head of intellectual property at purpose-led independent law firm Brabners, explore the key legal considerations for businesses looking to seize the opportunities presented by additive manufacturing.
Additive manufacturing – the construction of a 3D object from a digital model – represents one of the most exciting technological developments for manufacturers in decades.
Also known as 3D printing, the method is already revolutionising how businesses across the economy are designing, prototyping, testing, customising and ultimately assembling products, all the while delivering considerable cost, time and resource savings.
As such, the technology is poised to play a pivotal role in the advancement of the aerospace sector – indeed, industry leaders including Airbus, Boeing and Rolls Royce have already invested millions in bolstering their competitiveness in the space.
As outlined by a new report from the Aerospace Technology Institute (ATI), the UK possesses all of the resources, talent and technological expertise to embrace the technology and capitalise on a market that is expected to be valued at £10bn by 2033.
However, the report also suggests that a failure to make key advancements in supply chain resilience, education, efficiency and application by 2028 would hinder UK aerospace’s efforts to remain globally competitive.
As they strive to meet this deadline, businesses looking to adopt the technology must ensure they’re taking the necessary regulatory steps to allow them to make the most of the opportunity.
Patent pending
The key draw of additive manufacturing is its ability to create physical objects from digital models, allowing businesses to quickly and simply draw on the expertise and innovation of businesses around the world. This brings almost unfettered potential to revolutionise the product development process.
The process lends itself particularly well for the production of aerospace parts, which traditionally consists of multiple components and must be casted before use. Using 3D printing negates the need for this, allowing complex part assemblies to be completed in a single step and allowing manufacturers to develop a lighter final product.
Aerospace is an inherently innovative sector, and this ability to rapidly create and test new prototypes is accelerating the part innovation process, which has historically been incredibly time and resource intensive.
With this in mind, it’s important to be aware of the intellectual property rights associated with these digital blueprints. For example, if a manufacturing firm owns a registered design and/or patent, it has the exclusive right to make, use sell, import or export any product embodying that design.
As such, manufacturers utilising third party CAD drawings must ensure that they have the appropriate permissions and licensing agreements in place, or risk facing legal consequences. Similar issues are likely to arise in relation to any copyright and trade mark infringement.
On the other hand, a failure on the part of the design owner to secure appropriate intellectual property rights could present the opportunity for third parties to profit from use of a business’ product blueprint and innovation. For a business that has invested significant time and resources into research and development, such a failure to protect this investment could cause a product to lose its exclusivity, removing a significant barrier to market for competitors and weakening or destroying any intellectual property rights that the business might have had, so securing these protections is a key step.
It’s worth noting that there are unregistered rights that arise around a product automatically, such as copyright and unregistered design. However, these can be harder and more costly to enforce through litigation than the monopoly right created by registered intellectual property such as patents, registered designs and trade marks.
Material world
Additive manufacturing also brings the potential for businesses to design and produce parts with materials that would previously have proved impossible. For aerospace businesses, this grants the ability to deliver components with improved fuel efficiency, enhanced thermal management and reduced mass, while drastically cutting development cycles and reducing the overall time to market.
However, production teams utilising new materials need to be mindful of the necessary regulatory guardrails in place to ensure their effective and safe use – especially in the aerospace sector, where a failure to comply could have drastic consequences.
Despite being a relatively new technology, there are already several international material quality standards in place for the use of 3D printed components in aerospace. These range from ISO/ASTM 52910, which offers guidelines for using additive manufacturing in product design to AS9100, which measures manufacturers’ abilities to produce components which meet the industry’s most rigorous safety requirements.
Compliance with these standards is essential for any business looking to make the most of the technology.
Environmental potential
By reducing the resources spent on product development and minimising waste, additive manufacturing can deliver considerable sustainability benefits, meaning that it could play an integral role in aerospace’s industry-wide commitment to achieve net zero by 2050.
Yet if implemented incorrectly, the process can also be considerably damaging to the environment. For example, the 3D printing process involves moulding and burning complex plastics, which can produce dangerous emissions that must be properly dealt with via appropriate ventilation and air control methods.
In a similar vein, businesses must also ensure that they remain compliant with regulation around the proper disposal of waste materials, or risk facing fines and further penalties.
Ready for take-off?
We’re at a critical juncture in the progression of aerospace manufacturing, with innovations such as additive manufacturing becoming more commonplace alongside the use of AI and digitalisation.
As the home to innovative businesses and institutions such as the University of Sheffield’s Advanced Manufacturing Research Centre (AMRC) and The National Graphene Institute, the North is well positioned to be at the forefront of this transformation.
Time is ticking down before the ATI’s 2028 deadline though – and the onus is now on the region’s businesses to ensure they are prepared to capitalise on the opportunity.
For more information on how Brabners’ regulatory and professional conduct and intellectual property teams can support your business, contact claire.burrows@brabners.com or colin.bell@brabners.com
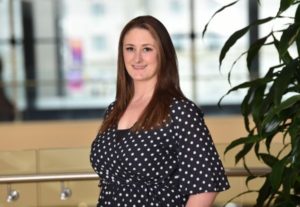
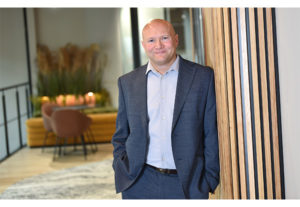